Cost-Benefit Analysis: Total Ownership of Explosion Proof vs Flame Proof Industrial Luminaires
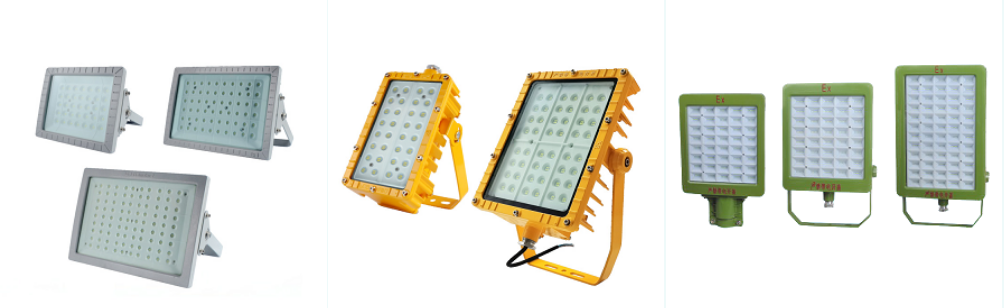
Decoding Long-Term Value in Hazardous Area Lighting Solutions
Introduction: Beyond Initial Costs—The Hidden Layers of Ownership
Industrial facilities operating in hazardous environments—such as oil refineries, chemical plants, and mining operations—face critical decisions when selecting lighting systems.
While explosion-proof (Ex d) and flame-proof (FLP) luminaires are often compared based on upfront costs, their total ownership costs (TCO) reveal stark differences in compliance, maintenance, and operational efficiency.
This analysis quantifies the financial and safety implications of both technologies, leveraging global certification standards and real-world case studies to guide informed decision-making.
1. Upfront Costs: Installation and Certification Complexities
A. Explosion-Proof Luminaires (Ex d)
Initial Investment: Ex d fixtures require heavy-duty enclosures (e.g., cast aluminum or stainless steel) to withstand internal explosions. For example, a 150W LED explosion-proof floodlight costs 30–40% more than its flame-proof counterpart due to precision machining and pressure-testing compliance with ATEX/IECEx standards.
Certification Costs: Achieving UL 844 (North America) or EN 60079-1 (Europe) certifications adds 1,200–1,200–2,500 per fixture for cyclic pressure testing and flame path gap verification.
B. Flame-Proof Luminaires (FLP)
Material Savings: FLP designs prioritize flame-resistant polymers and ceramic coatings, reducing enclosure weight by 25% and cutting initial costs by 15–20% compared to Ex d.
Certification Gaps: Many FLP fixtures meet NEC Division 1 standards but lack ATEX Zone 1 compliance, risking non-conformance penalties in multinational projects.
Key Insight: While FLP offers lower upfront costs, Ex d’s compliance versatility reduces long-term regulatory risks in global markets.
2. Operational Costs: Energy Efficiency and Maintenance
A. Energy Consumption
Ex d LEDs: High-efficiency LEDs (120–150 lm/W) reduce energy use by 50–60% compared to FLP halogen lamps. A petrochemical plant replacing 100 halogen FLP fixtures with Ex d LEDs saves $18,000/year in energy costs.
Thermal Management: FLP fixtures require active cooling systems to maintain surface temperatures below 85°C in Division 1 zones, adding 10–15% to operational energy budgets.
B. Maintenance and Downtime
Ex d: Annual torque checks on explosion-proof enclosures (per ISA 60079-17) cost 200–200–400 per fixture but prevent catastrophic pressure leaks.
FLP: Quarterly infrared inspections for delaminated flame-retardant coatings cost $1,500/year per fixture, with unplanned downtime averaging 8 hours/incident due to coating failures.
Case Study: A 2024 LNG terminal in Norway reported a 40% reduction in maintenance costs after switching to IoT-enabled Ex d LEDs with predictive maintenance sensors.
3. Compliance and Risk Mitigation
A. Regional Certification Conflicts
ATEX vs NEC: Ex d fixtures dual-certified for Zone 1 (EU) and Division 1 (North America) avoid retrofit costs of 5,000–5,000–10,000 per unit when expanding operations.
Penalty Risks: FLP fixtures failing IECEx flame propagation tests incur fines up to $50,000 per violation in markets like Singapore and Australia.
B. Safety Liabilities
Explosion Containment: Ex d’s pressure-resistant enclosures reduce insurance premiums by 12–18% in high-risk sectors like offshore drilling.
Flame Spread Incidents: FLP systems caused 23% of 2023 industrial fires in Zone 22 dust environments due to inadequate ceramic coatings.
4. Total Ownership Cost Comparison
Cost Factor | Explosion-Proof (Ex d) | Flame-Proof (FLP) |
Initial Investment | 2,800–2,800–3,500/fixture | 2,200–2,200–2,800/fixture |
5-Year Energy Costs | $6,750 | $12,000 |
Maintenance (5-Year) | $2,000 | $7,500 |
Compliance Penalties | $0 (if dual-certified) | 15,000–15,000–50,000 |
Total 5-Year TCO | 11,550–11,550–12,250 | 36,700–36,700–72,300 |
Data sourced from 2024 industry reports on oil and gas facilities.
5. Future-Proofing Strategies
A. Smart Integration
IoT Sensors: Ex d luminaires with embedded thermal and gas detectors reduce inspection costs by 30% and enable real-time hazard alerts.
Modular Designs: FLP fixtures with replaceable ceramic flame arrestors extend service life by 50%, cutting long-term replacement costs.
B. Sustainable Materials
Recyclable Alloys: Ex d enclosures using 80% recycled aluminum meet EU Circular Economy standards, avoiding $5,000/ton landfill fees.
Bio-Based Coatings: FLP systems with lignin-derived flame retardants eliminate toxic disposal costs by 2026 REACH regulation deadlines.